Do you want to access to this and other private contents?
Log in if you are a subscriber or click here to request service
Eaton brings Industry 4.0 to Turri's bakery machines
Solutions for specific production needs, with high levels of performance and flexibility
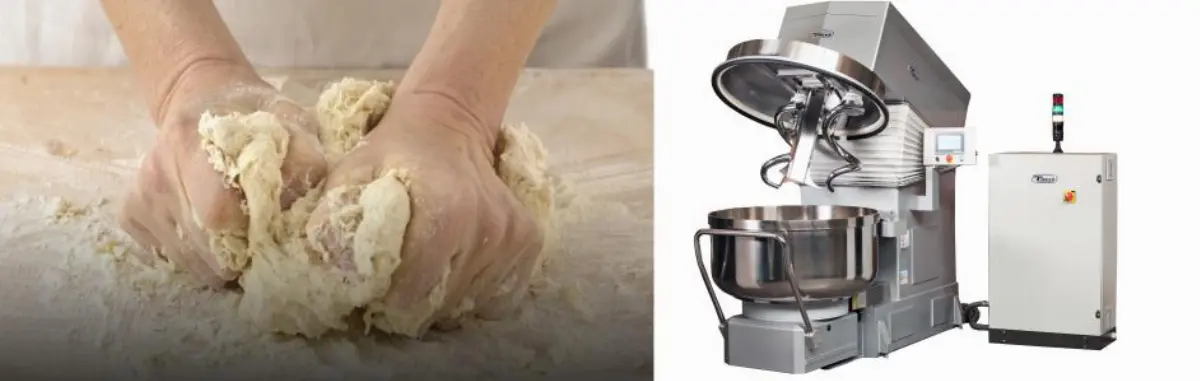
Italian Turri F.lli srl, which has been designing and manufacturing machines for bakeries, pasta factories, pastry shops and pizzerias since 1960, has chosen the American multinational Eaton to automate and digitize the bakery systems, enable the remote control and management of the machines and reduce their unwanted stops. Turri specializes in the development of machinery for important producers and...
hef - 17744
EFA News - European Food Agency
EFA News - European Food Agency