Do you want to access to this and other private contents?
Log in if you are a subscriber or click here to request service
Perugina, "Baci" more sustainable thanks to trigeneration
New installation in the San Sisto plant improves energy efficiency
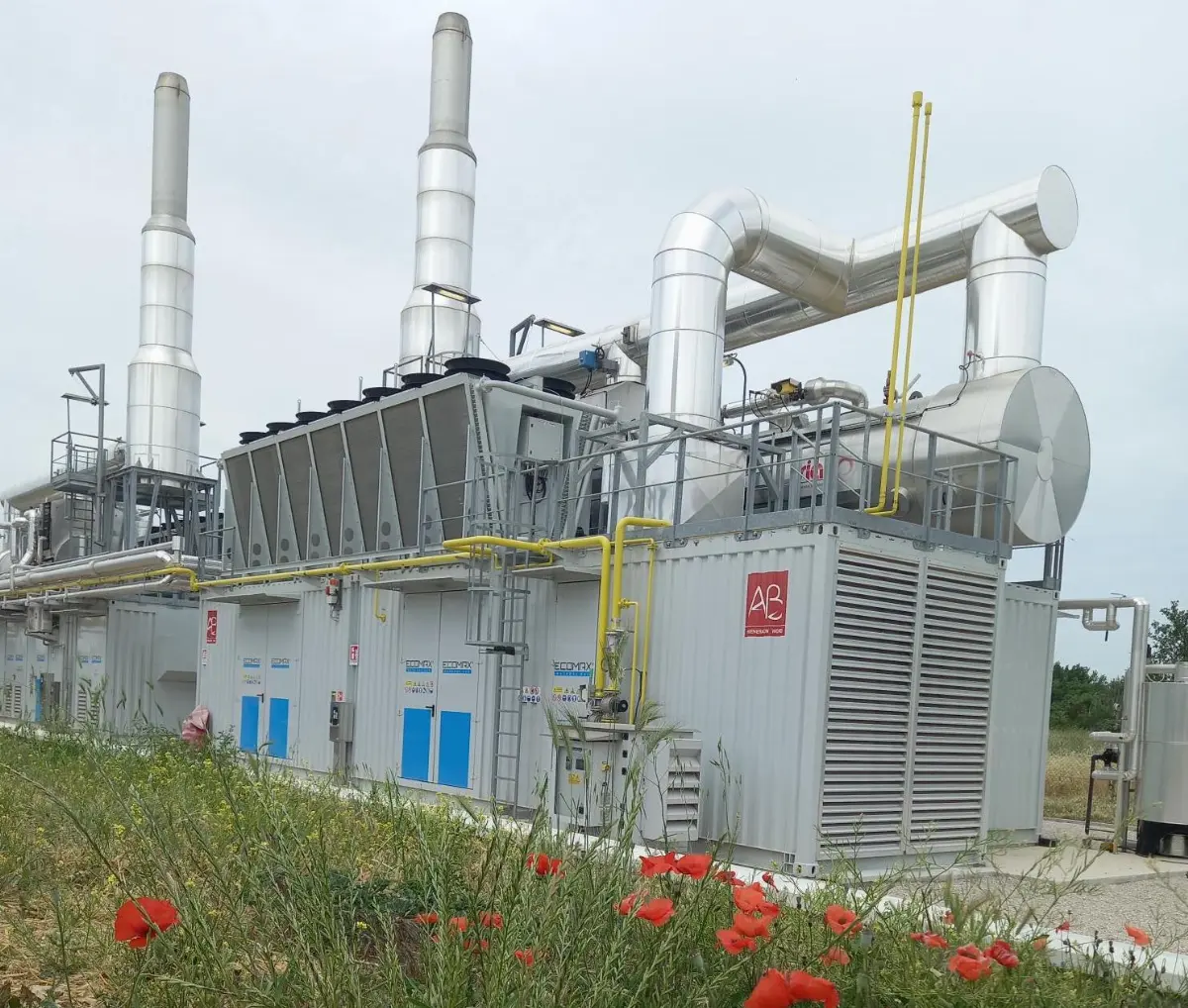
After having reduced about 45% of Nestlé's CO2 emissions in the last 10 years, thanks to the recent installation of the new AB trigeneration plant at the Perugina plant in San Sisto (Perugia), the group has taken a further step towards a increasingly efficient use of energy. The installed trigenerator consists of two 3.3 MW and 2.7 MW electrical power groups. Each group is composed of an internal c...
red - 25556
EFA News - European Food Agency
EFA News - European Food Agency